The need of highly qualified employees who knows how to work with these kinds of sensitive machines, the fear of having an unreliable machine because of lack of maintenance, or your machine is not working and need an expert to save time, which is one of the most valuable factor in the industry?
There are many occasions where our customers rely on our services. Our experienced, well trained team is always here to support you whatever the reason is.
Support
We are in close cooperation with you during the entire project, in the RFQ- and product development- phase as well. We ensure you full support before- and after the installation. If any changes arise after the design freeze or maybe after the production line is installed we remain at your disposal to help ... you out in challenging times as well. We will also be there for you after the warranty period if you have a problem to solve, a question that needs to be answered, or any kind of request.
Remote support is one of the tools which are necessary and could save the day in case there is an issue with the machine or with the communication not necessarily from our side.
We also provide cycle optimization and improvement of the cycle time. There are always possibilities to improve a machine to get faster cycle times, test more pieces at once, etc. There might be a need only to change the process due to new testing requirement. We are here for you.
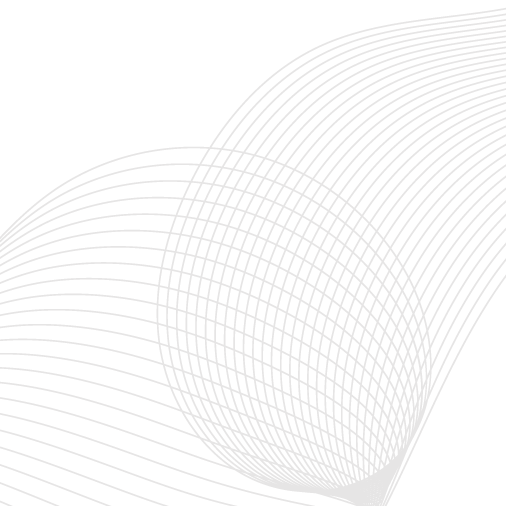
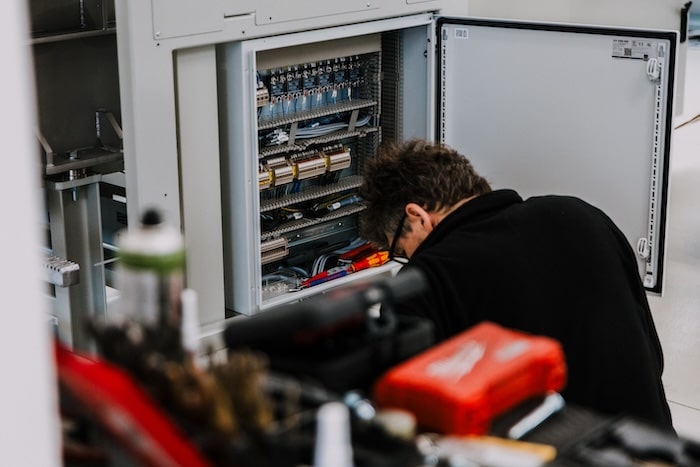
Retrofit
If the system is too old and you don’t find spare parts for the components, or if the components don’t match with your standards, or if the performance is not enough, but you don’t have enough budget for a new machine, your solution might be a retrofit. You can change the complete controls of the ... system (with the complete electrical cabinet, display and program) or change only the pumps, the adaptation, or anything what is needed to improve the production.
A retrofit doesn’t always mean changing the complete controls of your existing system, a retrofit is also done for smaller modifications such as when receiving a new product.
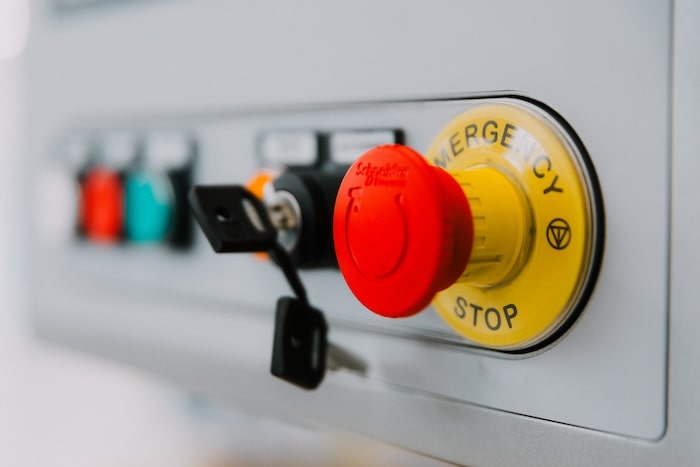
Training
We can offer vacuum technology training in different levels. The training courses are completely customized to your needs. The most common training courses are aimed at electrical and mechanical technicians as well as engineers. The training objective varies from the basics of vacuum technology to the ... special parts/functions of a dedicated machine or process.
To all our machines we provide trainings during the final acceptance phase for our customers to ensure a smooth operation. It is important to understand how the system works and to have the necessary knowledge during daily, weekly checkings of the given components, or in case of troubleshooting.
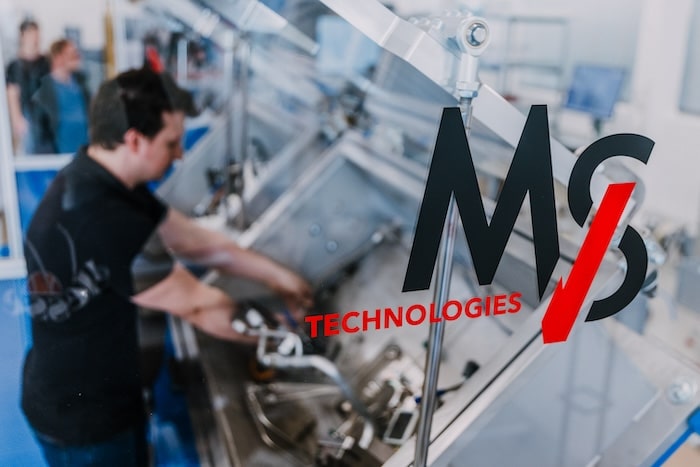
Maintenance
In order to ensure a stable production without malfunctions and breakdowns, the machines need to be kept in a perfect condition. During and after the warranty period, the maintenance – according to the maintenance plan – of the system is highly recommended.
These kinds of machines are very sensitive due ... to the fact, that we are measuring a leakage inside the system which can be disturbed by any additional leakage caused by dirty- or damaged- sealings or reduced performance of the pumps and the leak detector.
To be able to plan the service intervals and the expenses of the maintenance we can assist you with a maintenance contract in which we ensure you with our full support within the signed period. Don’t hesitate to contact us for any kind of requests regarding spare parts or components related to helium leak detection machines.
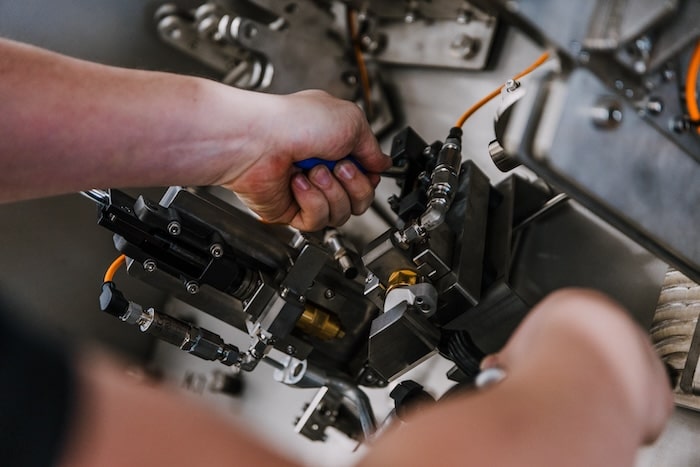
Support of product development and pre-series testing
We are here for you during the prototype- and product-development phase as well. In this critical phase we can be at your assistance, whether it is a design problem that needs to be solved to improve testability or just some early tests, that need to be done to see the result from the pre-series products.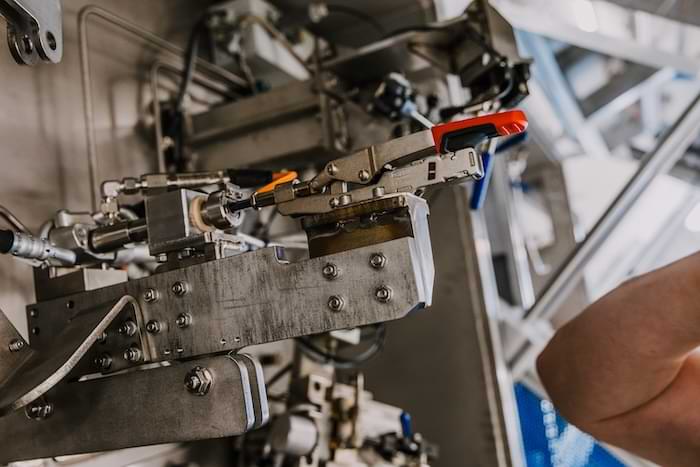